Innovative Construction
The construction industry would like to make changes by implementing “Construction 2.0” advocating “Innovation”, “Professionalisation” and “Revitalisation” to uplifting the efficiency and sustainability of the industry, increasing productivity, enhancing supervision and quality assurance, improving site safety and reducing environmental impacts.
In this regard, as a pioneer in innovative technologies within the construction industry, CKR has introduced and implemented various innovative construction methods in the CKR contracts.
Smart Site Management Hub (SSMH)
- 6–in-1 to provide holistic overview and enhance site management
- Closely monitor site daily operation and performance
- Real-time incident report and handling
- Automatic alert to avoid accidents
Integrated Digital Works Supervision System (iDWSS)
- Web-based centralised portal
- Integrate data from different CKR contracts
- View dashboard and reports anytime, anywhere
- Strengthen works supervision
- Enhance safety, efficiency and quality performance
Smart Over-Height Vehicle Detection System (OVDS)
- Detect over-height vehicles, avoid them hitting the temporary portal frame for bridge construction
- Automatic text message to alert construction team
- Display vehicle registration mark and warning message
Building Information Modelling (BIM)
- Adopt 4D construction method to simulate the actual working conditions and safety measures etc.
- For constructability review to reduce abortive works and potential risks
Skidding Mega Trusses
- Application of Design for Manufacture and Assembly (DfMA)
- Assemble, transport and install truss struts by skidding system
- Reduce on-site assemble works
- Minimise workers’ works over water and at-height
Early Rain/Tide Alert System
- Alert system integrated with Smart Site Management Hub (SSMH) and smart helmets
- Allow prompt evacuation before extreme weather
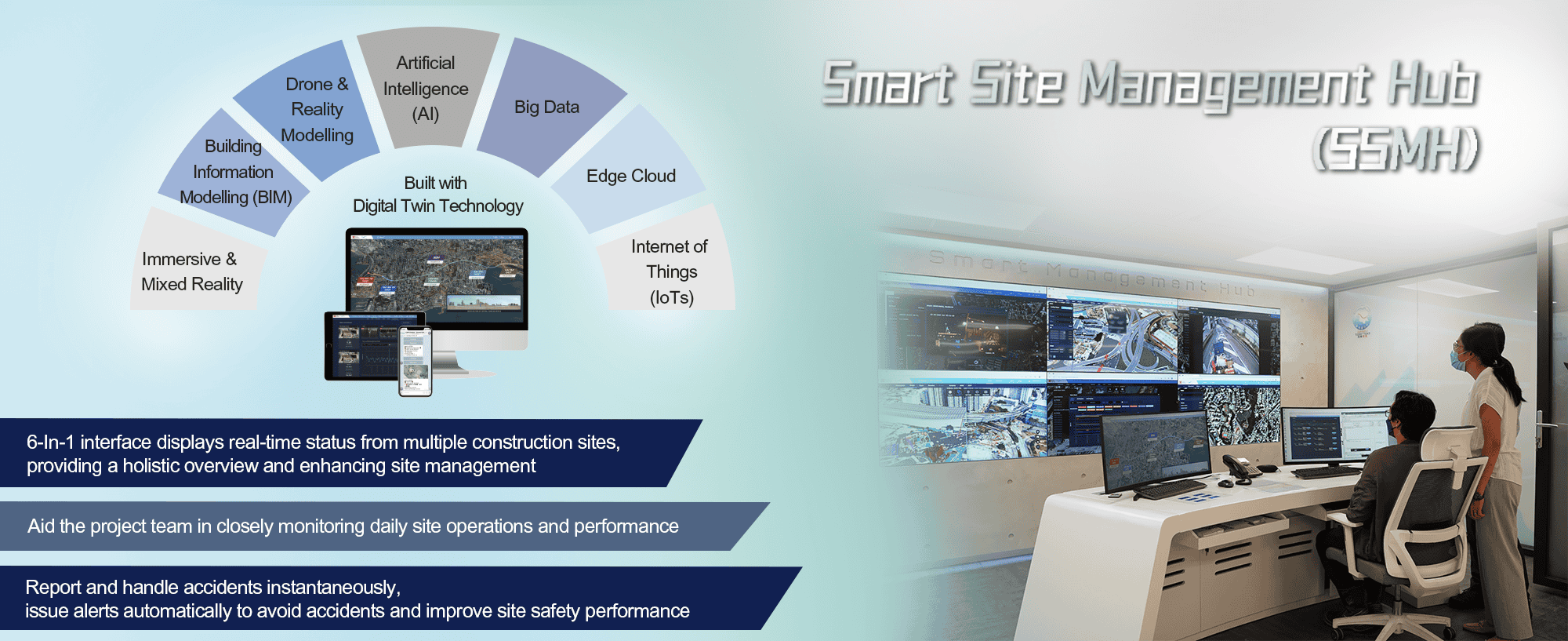
Central Tunnel – Smart Initiatives

Wi-Fi Backbone Network
- Extend Wi-Fi network coverage to underground tunnel
- Maintain seamless communication between underground and surface operations

Automatic Canopy Installation System
- Remote controlled safe canopy pipes connection
- Minimise the risk of finger and palm injuries

Artificial Intelligence (AI) Camera on Tunnel Wheeled Vehicles
- Anti-collision system and set detection zone
- Audible alarm and flashing signal

Next Generation of Tunnel Lining Shutter
- Remote hydraulic-controlled metal formwork
- Faster cycle and less manpower requirement

Asset Management System
- Access the record of lifting gears anytime and anywhere with QR code

Worker Management System
- Track workers’ location with smart helmets
- Optimise workforce deployment and facilitate rescue operation
BIM is adopted for generating three-dimensional models by digital representation throughout the construction period, facilitating the project team in making accurate judgments. BIM demonstrates actual building components of the whole structure by combining numerous working drawings and information, which enables the provision of relevant information to the project team during the construction stage. It can increase certainty, provide low-risk designs, reduce wastage, improve delivery on our projects, and enhance communications among the project team.
Through BIM, the project team perform a variety of analysis to enhance the construction quality by optimising the planning and design as well as improving coordination.
啟德通風大樓及行政大樓施工模擬

海台建造縮時模擬

YMTE - BIM vs Reality Model

油麻地停車場拆卸模擬

Under the Central Tunnel contract, the Contractor is required to carry out, amongst other things, the construction of an approximately 2.8km-long dual 3-lane tunnel. In order to enhance safety performance and to avoid risk of personal injury during the installation of temporary canopy supports at fault zones and tunnel portals, the project team has pursued an alternative construction methodology, namely automatic canopy installation system, which reduces labour intensiveness of the canopy installation process. This system provides a fully mechanised installation of canopy pipes which allows remote controlled operation for the safe connection of canopy pipes. Meanwhile, it saves the workers from direct contact with the moving hydraulic drilling machine. It is worth mentioning the system is the first-ever application in Hong Kong.

